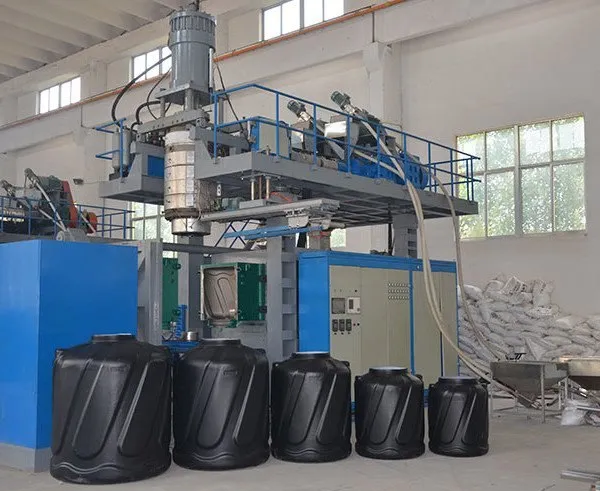
When you look at the market now in the world, plastic Water Tank Blow Moluding Machine is a very competitive, highly selling, and well-liked commodity. There are several reasons for its competitiveness.
- The government’s pipeline water supply is insufficient.
- There is no piped water supply available in rural areas.
- People continue to use the natural water supply.
Plastic water Tank Blow Moluding Machines are extensively used to hold water for the reasons mentioned above. Plastic water tanks should have particular properties for higher consumption. The attributes are: simple to install, high hygiene, and no rusting. Lightweight, long life (can withstand UV rays). Each plastic component needs a unique manufacturing procedure, which varies greatly depending on the product. Plastic bottles, containers, and other hollow objects are made by blow moulding.
The procedures for injection stretch blow moulding and blow moulding are combined.
For a threaded bottle neck, the plastic is first moulded into a solid preform. The preform is inserted into a stretch blow mould machine when it has cooled. The preform is then forced with pressurised air blown into a plastic container after being reheated with an infrared heater.
Blow moulding and injection moulding are two essential procedures in the manufacture of plastics. A wide number of industries, including the automotive, food service packaging, electronics, medical devices, irrigation, dental, energy, and environmental sectors, employ the products produced by these processes.
We have put up a summary of the primary types of blow moulding techniques used by plastics producers to help you better understand the various manufacturing methods available for your project.
Table of Contents
The Technique of water Tank Blow Moluding Machine
The raw plastic material is formed into a parison, which is a hollow tube with one open end, during the blow moulding process. Compressed air is injected into the parison after it is pressed into a metal mould that has been allowed to cool. When the created plastic cools and solidifies, the metal mould cracks open and releases the product.
This procedure has two subcategories: accumulator (erratic) extrusion blow moulding and continuous extrusion blow moulding. The device constantly extrudes plastic during continuous water Tank Blow Moluding Machine. In accumulator extrusion blow moulding, a reservoir is filled with plastic by the extruder over a predetermined period of time; after the reservoir is full, a ram is actuated to push the plastic through the extrusion head.
An EBM machine can produce a wide range of bottles, containers, and forms that are frequently used to generate things we use every day, like shampoo, oil bottles, peroxide bottles, and personal care items. Accumulator EBM machines are frequently used to produce huge components or goods that need thick walls, including gallon-sized water coolers and gasoline drums.
Best water Tank Blow Moluding Machine advantages
- German die head made with cutting-edge technology There is no leakage and the wall thickness is uniform.
- To maintain a cool temperature, we have air conditioning in the panel box.
- the most recent mold-changing technology, which is significantly faster and easier to use than limit switches.